3 simple steps to reduce downtime and meet production targets

Downtime
means missed production targets. Especially when you are running your line all day, every day.
So how can you increase the uptime of your line?
One of the most cost effective ways is to assess your coding solution. Here are 3 easy ways to do this.
1. Choose the right equipment for your production environment
Coding can affect your production line’s reliability in a number of ways. Production environments in the chemicals industry vary greatly, from wet, dusty, dry or clinical conditions. Ambient temperature can vary at different times of year, while the risk of chemical spills can also be present, meaning coded packaging may have to be discarded.
The solution is to ensure your coders have been designed to deal with continuous operation in a wide range of settings. Any liquid or dust ingress into the printer could cause failures and downtime on the line, something you can do without if you are to hit your production targets.
Look at the IP rating of your coding equipment: IP55 coders will cope with wet environments, ensuring no liquid ingress into the printer; and IP65 coders will have an enhanced protection against dust. On very dusty lines you may even need to consider a positive air function on a printhead to prevent dust causing it to fail, which would mean downtime while you clean the printhead. And robust, solid state printheads are a real plus here as they require minimal intervention and are far more reliable than those which need dismantling for every clean. Before you buy, trial the printer on your line to test how it copes with your production line.
If you need the flexibility to move printers between lines, then consider portable printers which don’t need to be fixed to permanent air supplies for example, or mounted on a wall. Having a printer that can be quickly moved between different filling lines gives you more flexibility of operation.
And consider what inks you are using in your coder. If you are producing a range of products with different substrates then could one coder reliably print on all of your products? Universal plastic adherent inks will stay put on any type of plastic, even if they inadvertently come into contact with chemicals during production or end use; code integrity is important during production for internal traceability as well as for customers so make sure the coding solution you select meets this requirement. Pigmented inks are another solution for coding onto different colours of packaging, coming in a range of colours including yellow or grey which are particularly good for standing out on most colours. Laser coders will also deliver permanent, chemical-resistant codes on most materials and are a very flexible coding option to consider.
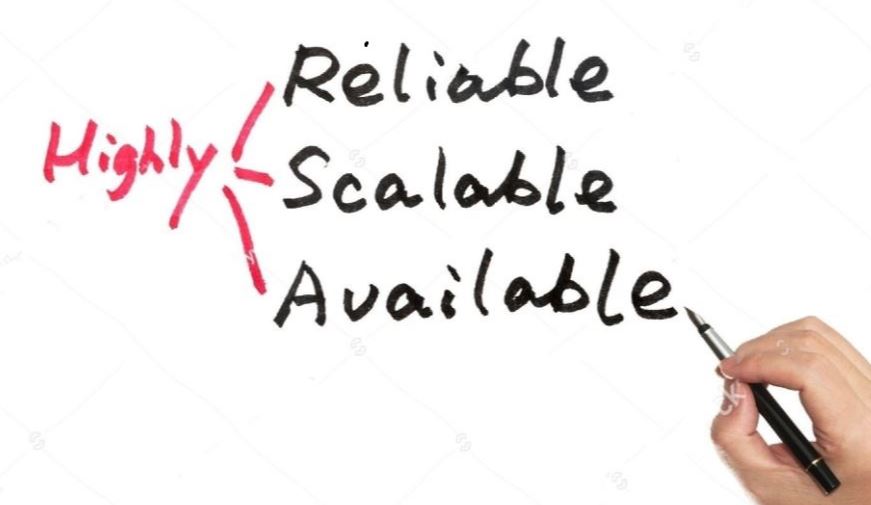
2. Reducing setup times
Coding can often be a bottleneck on a production line due to the time it takes to setup a coder at the start of the day, or between different product runs. Every minute it takes to set up a coder to print on a new product results in more downtime and therefore less profitability.
Chemical manufacturers are able to increase their profitability by combating unnecessary setup time using easy to operate coders. Simple WYSIWYG screens make code set ups quick and easy and also minimise operator errors, saving time wasted due to lost production. Having the settings for different lines programmed into the printer will make setup even quicker.
Additionally the ability to code in different orientations, for example on the side or underneath of the product, will allow for quick product line changeovers without switching between printers
3. Reducing servicing and maintenance
With the aggressive production targets typically found with chemical manufacturing, eliminating unnecessary downtime is essential for increasing profitability and reducing your cost-per-product.
Unnecessary downtime usually falls into two main areas: servicing or breakdown. Each of these mean the production line has to be stopped, and can cause lengthy delays to production, reducing profitability.
Coders with self-service options and long service intervals will reduce downtime on your line, and help you meet your targets of continual operation with a lower overall cost of ownership.
Find out more
If your coders are struggling to keep up with your production targets, find out more about how Linx’s coding solutions for the chemicals industry can help.
For our entire range of products click here.